SPE Automotive Composites Conference & Exhibition 2024
SPE ACCE 2024 - Cost Effective Thermoplastic Body Structures
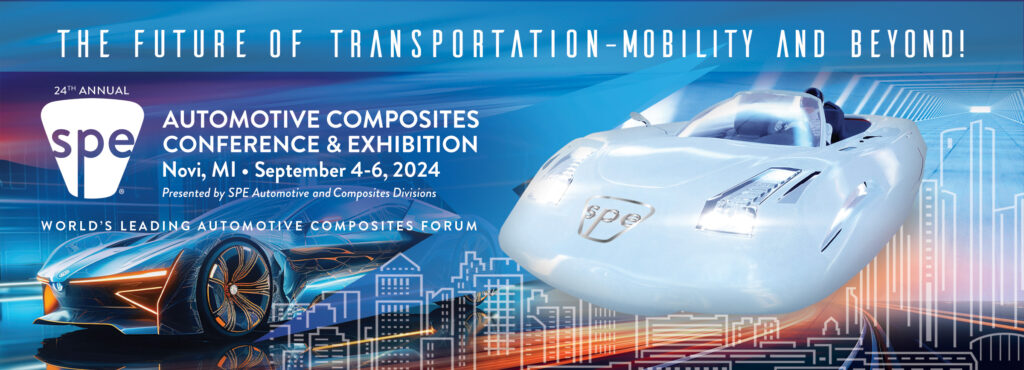
WEAV3D has developed a novel hybrid-material approach, Rebar for Plastics®, that combines existing thermoforming, compression molding or injection overmolding processes with woven composite lattices formed from unidirectional thermoplastic tapes to produce high-rate, cost-effective structural composites. The resulting structural panel exhibits high stiffness, strength, and ductility, equivalent or better than sheet metal, while offering weight savings of up to 65% compared to steel. In partnership with Braskem, Altair, and the Clemson Composites Center, an automotive door structure originally developed in carbon fiber/PA6 organosheet was redesigned as a lattice reinforced polypropylene panel. A case study covering design, manufacturing, and testing of this innovative thermoplastic composite structure will be presented, showcasing 20% weight savings and 50% cost savings vs. organosheet, while also reducing trim scrap mass by 63%. This presentation will also discuss how OEMs and Tier suppliers can adapt this cost-effective lattice-reinforced approach to other vehicle components and molding processes.
SPE Automotive Composites Conference & Exhibition 2024
SPE ACCE 2024 - Composite Lattice Reinforced Part Optimization with FEA: An Automotive Door Component Case Study
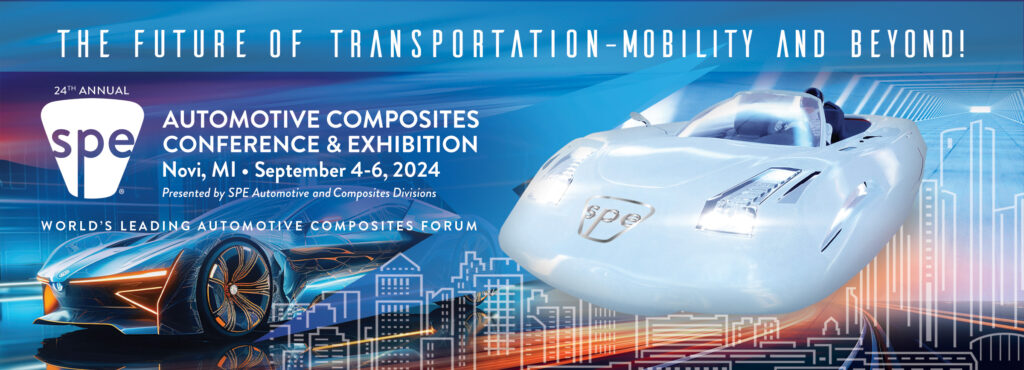
This paper presents a finite element analysis (FEA) method of modelling automotive components reinforced with WEAV3D composite lattice structures. WEAV3D Inc. has developed a novel hybrid-material approach, Rebar for Plastics®, merging existing thermoforming, compression molding or injection overmolding processes with woven composite lattices formed from unidirectional thermoplastic tapes to produce high-rate, cost-effective structural composites. These materials pose challenges for conventional composite FEA modeling, demanding advanced techniques for accurate mechanical predictions, especially in structural applications.
Presented FEA methodology addresses these challenges by enabling explicit modeling of lattice designs using Altair HyperMesh. By parameterizing tape materials, spacing, and layer count through scripting, the methodology streamlines design exploration, eliminating the need for CAD models for each iteration and enabling regional optimization within the part. This optimizes lattice structures efficiently to achieve desired mechanical properties at the part level.
Through a case study of an automotive door component, we demonstrate the applicability of our FEA workflow. Comparison of FEA predictions with experimental data validates the reliability of the model. These results highlight the efficacy of our methodology in predicting mechanical behavior, suggesting its potential to guide design decisions across various industrial applications through optimization.
ASME 2024 Aerospace Structures, Structural Dynamics, and Materials Conference
A Multiscale Approach to the Design and Analysis of WEAV3D Lattice Structures
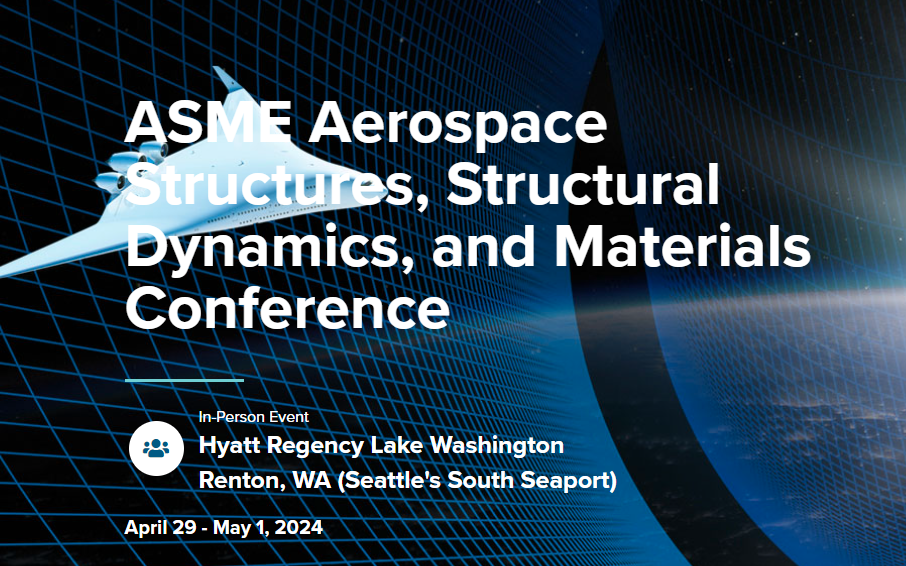
Altair Vice President of Composite Technology & Aerospace Strategy, Jeffrey A. Wollschlager presents “A Multiscale Approach to the Design and Analysis of WEAV3D Lattice Structures” at the ASME 2024 Aerospace Structures, Structural Dynamics, and Materials Conference.
ANTEC 2024 - Cost-Effective Automotive Body Structures
ANTEC 2024 - Cost-Effective Automotive Body Structures
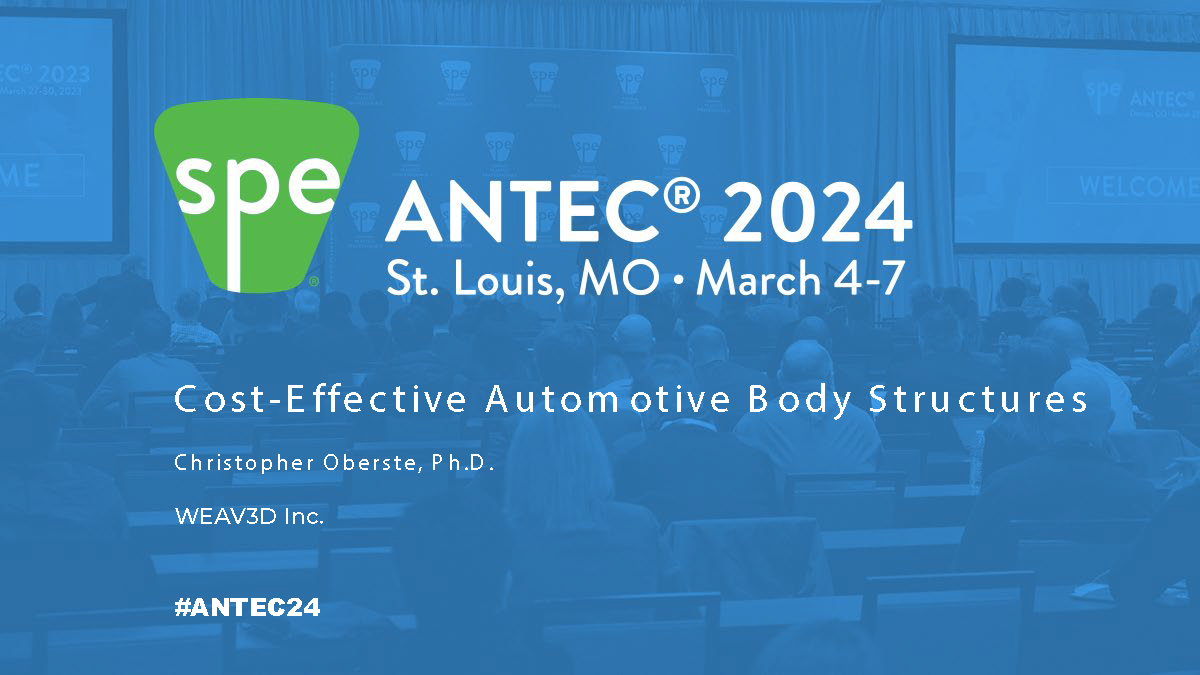
WEAV3D has developed a novel hybrid-material approach, Rebar for Plastics®, that combines existing thermoforming, compression molding or injection overmolding processes with woven composite lattices formed from unidirectional thermoplastic tapes to produce high-volume, low-cost structural composites. The resulting structural panel exhibits high stiffness, strength, and ductility, equivalent or better than sheet metal, while offering weight savings of up to 65% compared to steel.
In partnership with Braskem, Altair, and the Clemson Composites Center, an automotive door structure originally developed in carbon fiber/PA6 organosheet was redesigned as a lattice reinforced polypropylene panel. This highly optimized structure achieved 20% weight savings and 50% cost savings vs. the original organosheet, while also reducing trim scrap mass by 63%. The FEA design process and experimental results will be presented, as well as a cost and performance comparison against the original organosheet design.
Rebar for Plastics: Enabling Cost Effective Body Structures
Rebar for Plastics: Enabling Cost Effective Body Structures
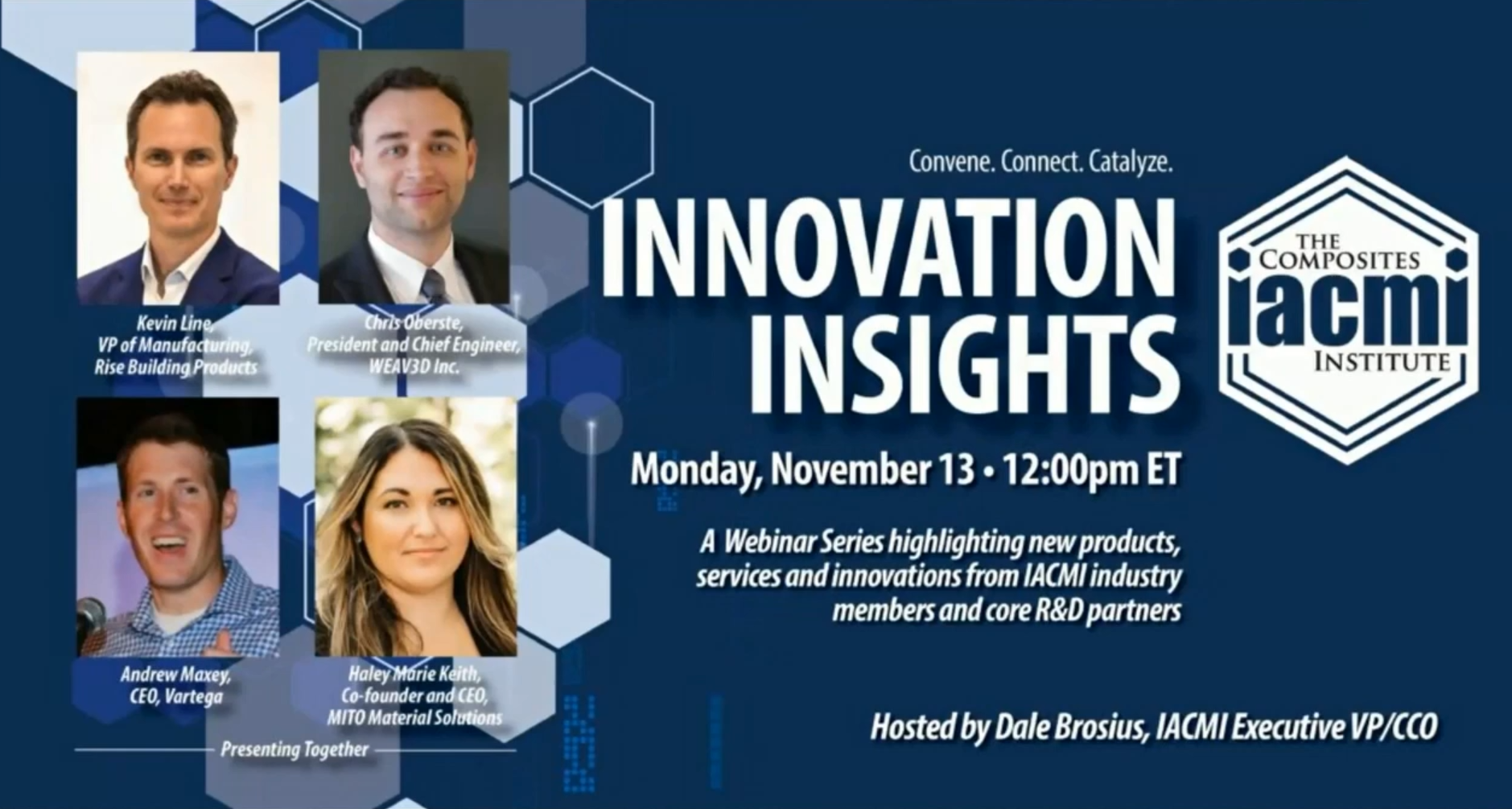
In partnership with Braskem, Altair, and the Clemson Composites Center, an automotive door structure originally designed in carbon fiber/PA6 organosheet was redesigned utilizing WEAV3D’s Rebar for Plastics® design methodology, which leverages various micro-and macro-mechanical concepts to maximize performance and minimize cost in hybrid length-scale composites. This highly optimized structure achieved 20% weight savings and 50% cost savings vs. the original organosheet, while also reducing trim scrap mass by 63%.
WEAV3D presents at CAMX 2023 in Atlanta, GA.
WEAV3D to present at CAMX 2023 in Atlanta, GA.
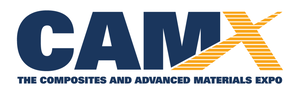
Rebar for Plastics – A Novel Approach to Part Optimization with Hybrid Length-Scale Composites
A Revised Finite Element Analysis Approach to Designs and Optimize Composite Lattice Reinforcements and Simulate the Mechanical Properties of Composite Lattice Reinforced Plastics
Structural Enhancement of Sustainable Materials
Structural Enhancement of Sustainable Materials
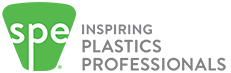
The automotive industry has committed to increasing the use of sustainable materials in order to meet long term embodied carbon and circular economy goals. “Sustainable” materials are not clearly defined, but generally include natural fillers and fibers, polymers produced from bio-renewable feedstocks, and post-consumer and post-industrial recycled polymers. While bio-renewable feedstocks are largely equivalent to petroleum-based feedstocks in final polymer performance, natural fibers and recycled materials suffer from reduced and inconsistent mechanical properties compared to their synthetic or virgin alternatives. A significant portion of plastic components in the vehicle today are glass reinforced, presenting a substantial performance barrier to the adoption of natural fibers.
WEAV3D has developed a novel hybrid-material approach, Rebar for Plastics®, that dramatically improves the performance of sustainable materials, through a combination of natural fiber reinforced polypropylene (NFPP) mats and woven composite lattices formed from unidirectional tapes.
Numerical Modeling of the Bond Behavior Between Thermoplastic FRP Lattice and Concrete
Numerical Modeling of the Bond Behavior Between Thermoplastic FRP Lattice and Concrete
Replacing steel bars with fiber-reinforced polymer (FRP) bars is widely acceptable as a potential solution to eliminate the corrosion problem in reinforced concrete structures. This paper examines another option to resolve this problem, which utilizes a novel composite lattice material manufactured by WEAV3D Inc. The composite lattice is manufactured by weaving and bonding thermoplastic FRP tapes using an innovative lattice-forming process. Accurate representation of the bond between this lattice and concrete is needed to be able to utilize it in structural concrete elements. In this paper, numerical modeling of the bond between WEAV3D composite lattice and concrete is examined. The model predictions were validated using experimental data.
Designing, Optimizing and Simulating the Mechanical Properties of Composite Lattice Reinforced Plastics With FEA
Designing, Optimizing and Simulating the Mechanical Properties of Composite Lattice Reinforced Plastics With FEA
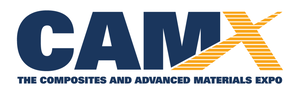
Recent advances in thermoplastic composite manufacturing have resulted in the development of hybrid overmolded composite structures, combining continuous fiber composites with injection or compression molded compounds; however, standard FEA techniques developed for isotropic materials and ply-based composites do not accurately capture the physical properties and material behavior of these hybrid materials.
Automotive Lightweighting 2021 June 14 to 15, 2021
Automotive Lightweighting 2021June 14 to 15, 2021
Cost-effective Weight Reduction with Multi-material, Hybrid Length-scale Composites
Combining multi-material continuous fiber-reinforced lattices with long fiber overmolding enables lighter, stronger and less expensive structural composites
Novel composite manufacturing process enables high throughput production of multi-material and locally optimized composite lattices
FEA case study that illustrates expanded design space provided by multi-materials, hybrid length-scale composites