Structural Enhancement of Sustainable Materials
Structural Enhancement of Sustainable Materials
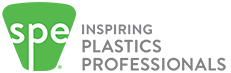
The automotive industry has committed to increasing the use of sustainable materials in order to meet long term embodied carbon and circular economy goals. “Sustainable” materials are not clearly defined, but generally include natural fillers and fibers, polymers produced from bio-renewable feedstocks, and post-consumer and post-industrial recycled polymers. While bio-renewable feedstocks are largely equivalent to petroleum-based feedstocks in final polymer performance, natural fibers and recycled materials suffer from reduced and inconsistent mechanical properties compared to their synthetic or virgin alternatives. A significant portion of plastic components in the vehicle today are glass reinforced, presenting a substantial performance barrier to the adoption of natural fibers.
WEAV3D has developed a novel hybrid-material approach, Rebar for Plastics®, that dramatically improves the performance of sustainable materials, through a combination of natural fiber reinforced polypropylene (NFPP) mats and woven composite lattices formed from unidirectional tapes.
Braskem Takes Polypropylene to the Next Level of Performance in Partnership with WEAV3D® utilizing its Rebar for Plastics® Lattice Technology
IMPROVING NATURAL-FIBER REINFORCED POLYPROPYLENE
This solution combines Braskem’s polypropylene sheets with WEAV3D lattice technology to address new structural and automotive applications requiring high-strength, lightweight material solutions
Braskem to present its PP solutions with WEAV3D lattice technology at the 2023 SPE® TPO Global Automotive Conference in Detroit, October 1-4
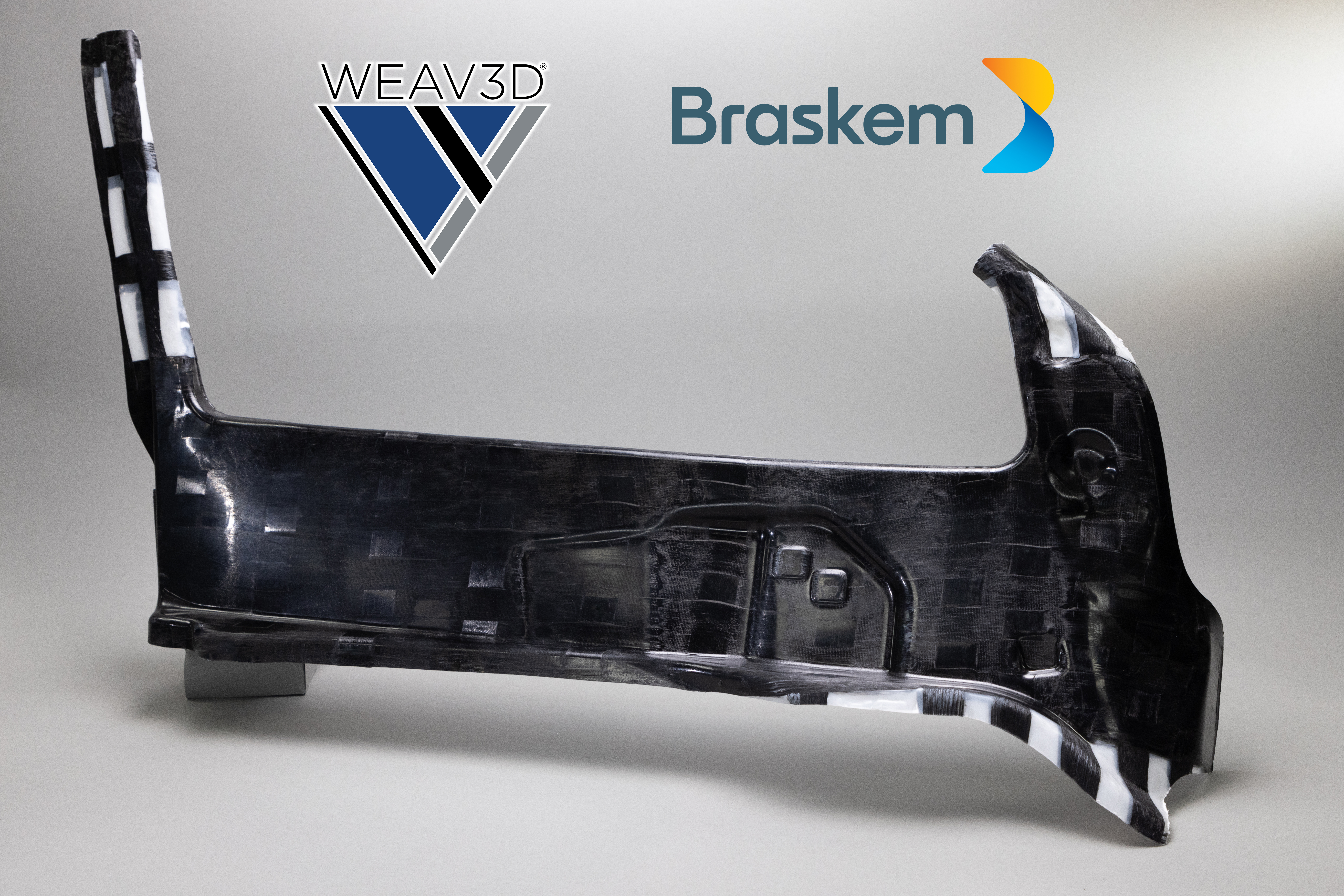
Numerical Modeling of the Bond Behavior Between Thermoplastic FRP Lattice and Concrete
Numerical Modeling of the Bond Behavior Between Thermoplastic FRP Lattice and Concrete
Replacing steel bars with fiber-reinforced polymer (FRP) bars is widely acceptable as a potential solution to eliminate the corrosion problem in reinforced concrete structures. This paper examines another option to resolve this problem, which utilizes a novel composite lattice material manufactured by WEAV3D Inc. The composite lattice is manufactured by weaving and bonding thermoplastic FRP tapes using an innovative lattice-forming process. Accurate representation of the bond between this lattice and concrete is needed to be able to utilize it in structural concrete elements. In this paper, numerical modeling of the bond between WEAV3D composite lattice and concrete is examined. The model predictions were validated using experimental data.
Designing, Optimizing and Simulating the Mechanical Properties of Composite Lattice Reinforced Plastics With FEA
Designing, Optimizing and Simulating the Mechanical Properties of Composite Lattice Reinforced Plastics With FEA
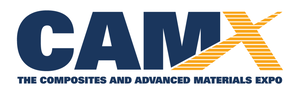
Recent advances in thermoplastic composite manufacturing have resulted in the development of hybrid overmolded composite structures, combining continuous fiber composites with injection or compression molded compounds; however, standard FEA techniques developed for isotropic materials and ply-based composites do not accurately capture the physical properties and material behavior of these hybrid materials.
Automotive Lightweighting 2021 June 14 to 15, 2021
Automotive Lightweighting 2021June 14 to 15, 2021
Cost-effective Weight Reduction with Multi-material, Hybrid Length-scale Composites
Combining multi-material continuous fiber-reinforced lattices with long fiber overmolding enables lighter, stronger and less expensive structural composites
Novel composite manufacturing process enables high throughput production of multi-material and locally optimized composite lattices
FEA case study that illustrates expanded design space provided by multi-materials, hybrid length-scale composites
WEAV3D presents at JEC Composites Connect June 1 to 2, 2021
JEC Composites Connect
June 1 to 2, 2021
JEC Composites Connect is the online meeting place for the global composites community.
This first JEC Composites Connect works as an online trade show with digital booths, a conference program, networking areas and JEC Group Innovation Programs.
Investigating the Relationship between Fiber Length, Volume Fraction, and Mechanical Properties of Fiber-Reinforced Plastics
Investigating the Relationship between Fiber Length, Volume Fraction, and Mechanical Properties of Fiber-Reinforced Plastics
Within the current reinforced plastic manufacturing paradigm, a paradox exists; filled and long-fiber-reinforced plastics are cheap, but lack the mechanical properties needed to displace structural metals, while continuous-fiber reinforced plastics (“CFRP”) possess exemplary mechanical properties but cost too much to compete with inexpensive stamped steel. A revolutionary approach is needed to enable vehicle designers to bridge this gap and restart the growth of plastics in automotive structures.
Novel Approach to Thermoplastic Composite Production Enables Localized Design Optimization
Novel Approach to Thermoplastic Composite Production Enables Localized Design Optimization
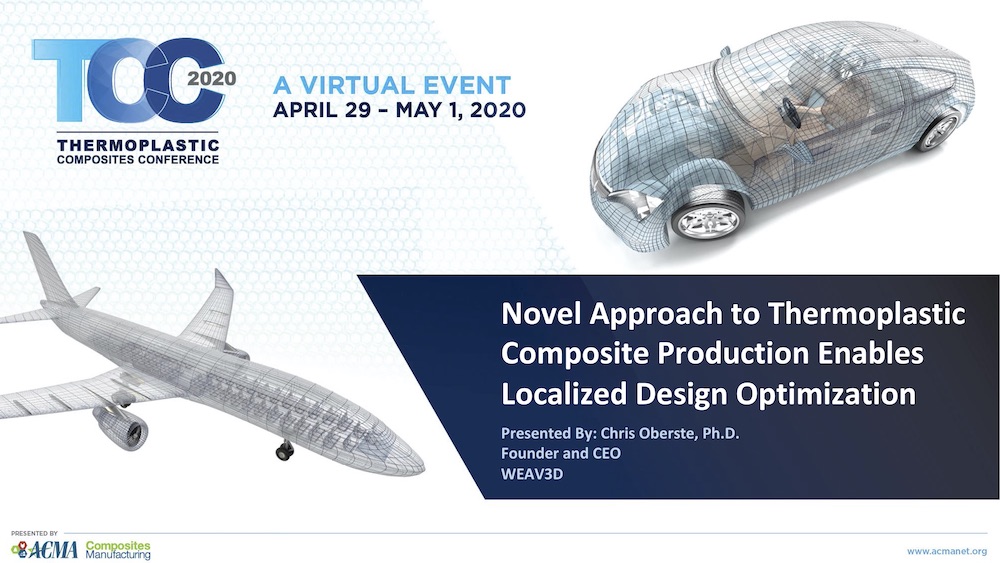