SPE ACCE 2024 - Composite Lattice Reinforced Part Optimization with FEA: An Automotive Door Component Case Study
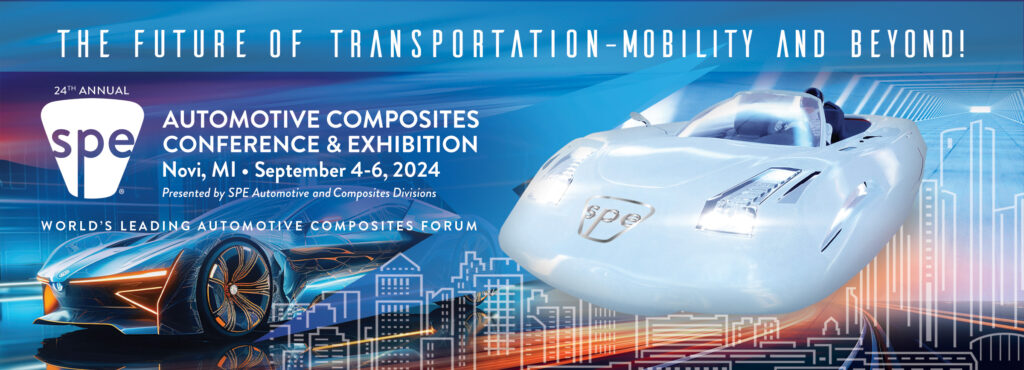
This paper presents a finite element analysis (FEA) method of modelling automotive components reinforced with WEAV3D composite lattice structures. WEAV3D Inc. has developed a novel hybrid-material approach, Rebar for Plastics®, merging existing thermoforming, compression molding or injection overmolding processes with woven composite lattices formed from unidirectional thermoplastic tapes to produce high-rate, cost-effective structural composites. These materials pose challenges for conventional composite FEA modeling, demanding advanced techniques for accurate mechanical predictions, especially in structural applications.
Presented FEA methodology addresses these challenges by enabling explicit modeling of lattice designs using Altair HyperMesh. By parameterizing tape materials, spacing, and layer count through scripting, the methodology streamlines design exploration, eliminating the need for CAD models for each iteration and enabling regional optimization within the part. This optimizes lattice structures efficiently to achieve desired mechanical properties at the part level.
Through a case study of an automotive door component, we demonstrate the applicability of our FEA workflow. Comparison of FEA predictions with experimental data validates the reliability of the model. These results highlight the efficacy of our methodology in predicting mechanical behavior, suggesting its potential to guide design decisions across various industrial applications through optimization.