Braskem and WEAV3D® Announced as Finalists for JEC Composites Innovation Awards 2024
Braskem and WEAV3D® Announced as Finalists for JEC Composites Innovation Awards 2024
Cost-effective automotive door body structure demonstrator part made from Braskem polypropylene and WEAV3D lattice technology receives industry recognition for a novel approach.
Braskem and WEAV3D automotive component to showcase at the 2024 JEC World trade show in Paris, France, March 5-7, 2024.
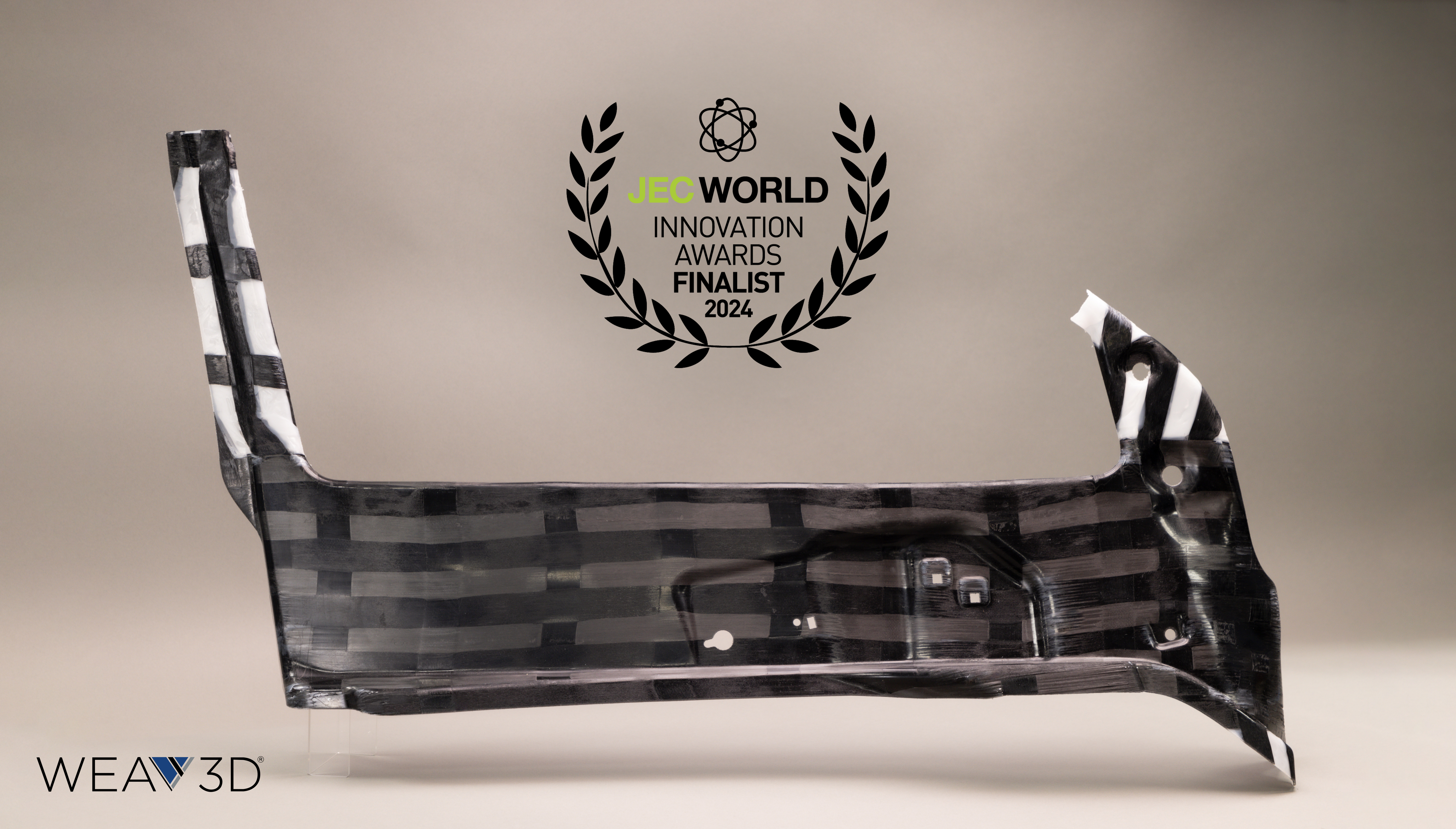
Braskem Takes Polypropylene to the Next Level of Performance in Partnership with WEAV3D® utilizing its Rebar for Plastics® Lattice Technology
IMPROVING NATURAL-FIBER REINFORCED POLYPROPYLENE
This solution combines Braskem’s polypropylene sheets with WEAV3D lattice technology to address new structural and automotive applications requiring high-strength, lightweight material solutions
Braskem to present its PP solutions with WEAV3D lattice technology at the 2023 SPE® TPO Global Automotive Conference in Detroit, October 1-4
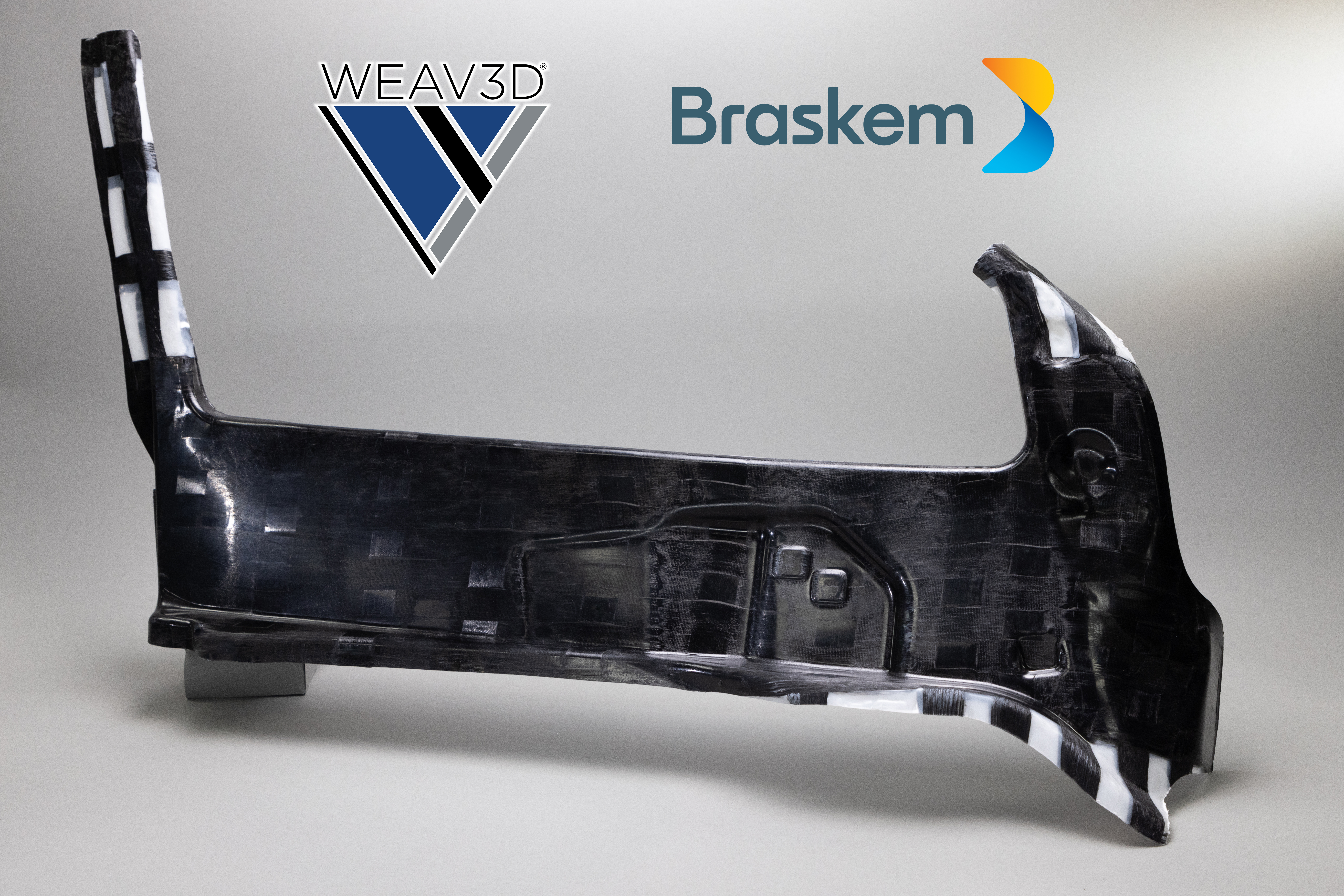
Advanced Commercial Delivery Vehicle Reinforcements
Our woven composite lattice technology can boost the fuel economy of commercial delivery vehicles through structural lightweighting. This Rebar for Plastics® approach is compatible with common plastic manufacturing methods, enabling optimizations of the mechanical properties of structural components—including impact resistance and stiffness. Watch our newest video for more information.
Improving Natural-Fiber Reinforced Polypropylene
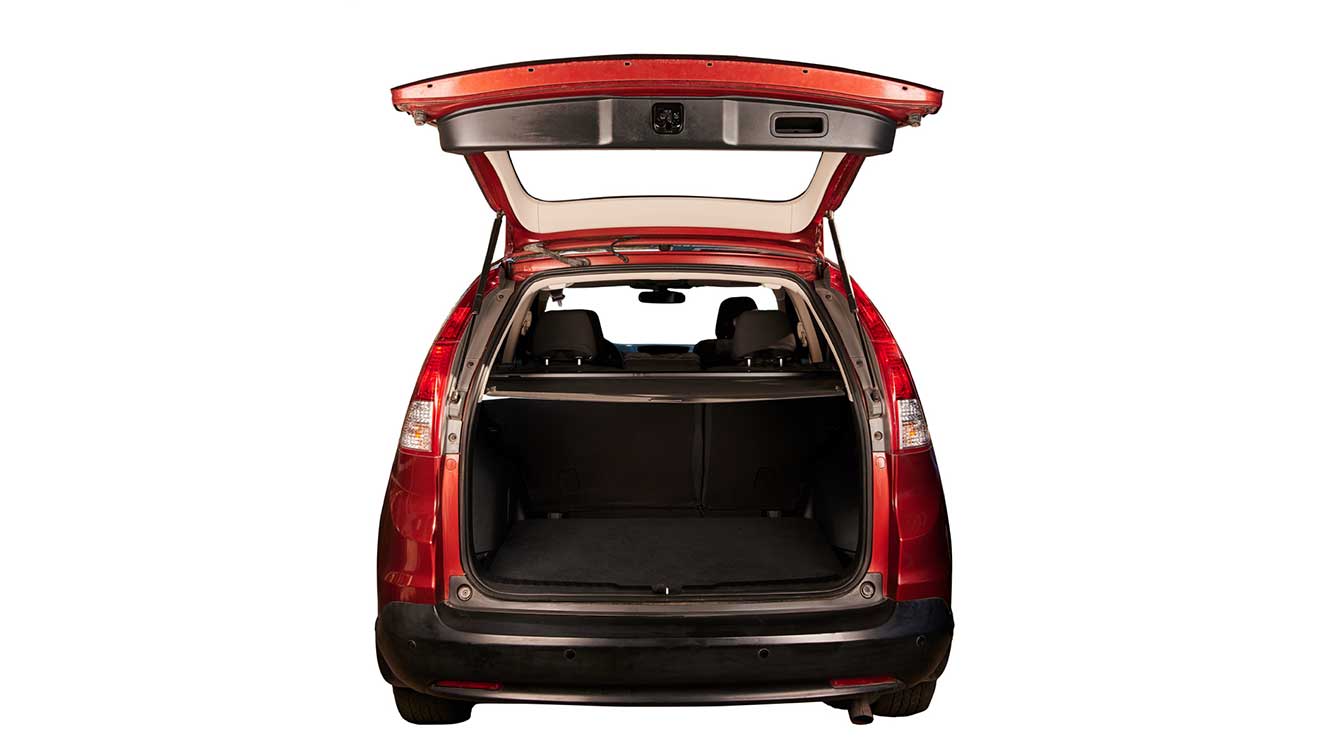
Natural-fiber reinforced thermoplastic composites have recently emerged as a lightweight, sustainable alternative to glass reinforced plastics for automotive interior applications. These materials, however, have traditionally lacked sufficient structural performance on their own to meet load and deflection requirements, necessitating the reinforcement of these materials with metallic or back-injected support structures.
This need for additional support adds a weight and cost burden that can be eliminated using our Rebar for Plastics® design approach. Download our application note to learn how the addition of WEAV3D® reinforcements produced dramatic improvements in strength, stiffness and energy absorption in natural-fiber reinforced automotive components.
New CompositesWorld Article Explores Our Technology in High-Volume Applications
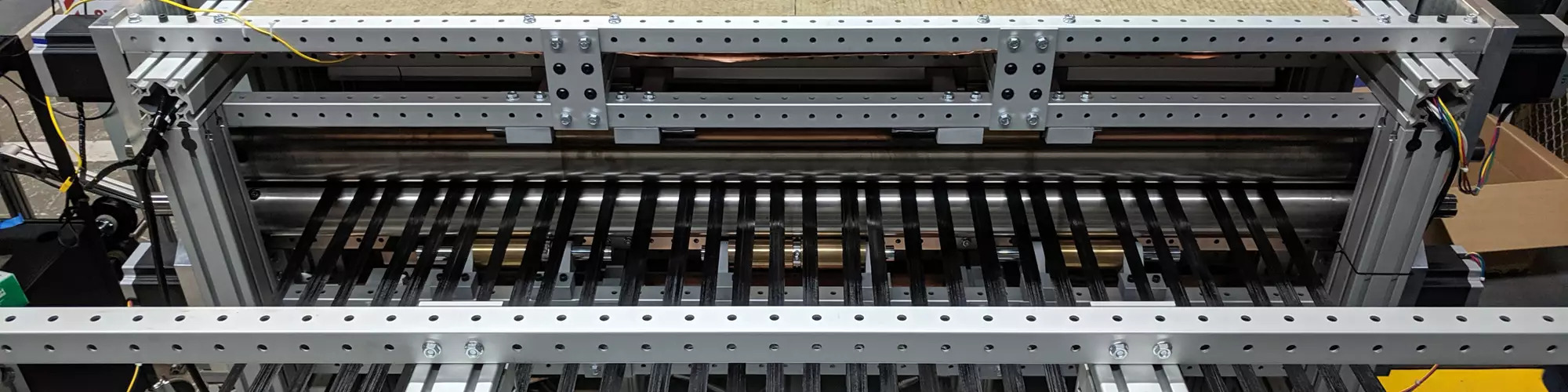
We’re excited to announce we were recently featured in CompositesWorld, a leading source of news and information about fiber-reinforced composites manufacturing. The article takes a deep dive into our locally tunable composite technology—from concept to commercialization.
The article interviews our founder and CEO, Christopher Oberste, who developed the initial concept for our woven composite lattice reinforcement technology while earning his PhD at the Georgia Institute of Technology. From there, the article follows Oberste’s efforts to commercialize the technology and grow WEAV3D into the company it is today.
While the initial plan was to qualify the materials as reinforcement structures in aerospace components, Oberste and his colleagues shifted focus to the automotive and construction markets once they discovered the need for cost-effective, lightweight parts in these industries. “[Companies in these markets] told us that most of the conventional composite manufacturing processes available weren’t able to provide the volume they needed at the costs they wanted,” Oberste tells CompositesWorld.
From there, the WEAV3D technology evolved to become an enabling solution for producing high-volume composite parts at low cost. The result is our Rebar for Plastics® design concept, which now has the following commercial applications:
- Construction: Our composite lattice enables manufacturers of utility products and construction accessories to produce economical, high-quality polymer concrete products, including trench systems.
- Automotive: Oberste and his team have started discussions with U.S. and European tier 1 automotive suppliers and OEMs about using WEAV3D products to reinforce plastic panels in vehicles.
To read the full CompositesWorld article, which takes a detailed look at our composite technology, weaving process and commercialization journey, click here.
WEAV3D Process Overview
The patent pending WEAV3D® process is based on a woven composite lattice reinforcement called Rebar For Plastics®. Our lattice forming machines produce custom lattice structures from unidirectional, fiber-reinforced composite tapes. The composite lattices are then overmolded into a finished structural component using conventional molding processes.
By tuning the weave density, tape materials and number of layers in the lattice preform, we can locally tune a part’s performance to meet application-specific targets, all while reducing costs by 30 to 50% versus traditional composites.
WEAV3D Applications
WEAV3D® technology reduces waste, cycle time and material handling costs—enabling new innovations in the automotive and construction industries. For example, our patent pending reinforcement materials let you lightweight automotive interior and exterior components, including instrument and body panels—increasing vehicle fuel economy and extending EV range.
Our composite lattice is also an alternative solution to traditional steel wire cage, rebar and sheet molding compound (SMC) reinforcement for precast polymer concrete. It offers a lightweight, completely non-metallic reinforcement material that provides high levels of durability and strength.
New Oldcastle Cable Trench Overcomes Challenges of Steel Reinforcement, Thanks to WEAV3D Composites
Cable trenches play an important role in managing and distributing cables and wires in utility, rail and power applications. Oldcastle, a leading provider of building materials, supplies these durable components in the form of its polymer-based concrete trench systems, which use a steel wire cage to reinforce the material. While they have their advantages, polymer concrete systems don’t adhesively bond to the steel—instead relying purely on the mechanical interface between the materials.
Our composite lattice has allowed Oldcastle to produce an economical, yet high-quality cable trench without the failure modes of polymer concrete systems. The result of our collaboration is a completely non-metallic cable trench system that offers many advantages. Read our recent application note to learn more.
Venture Atlanta Selects WEAV3D as Showcase Company at 2020 Conference
We’re excited to announce WEAV3D has been chosen to showcase at this year’s Venture Atlanta Online conference as one of the Southeast’s most promising technology companies. The event will bring together over 1,000 entrepreneurs, investors and leaders for the largest venture capital conference in the region.
As a showcase company, we’ve been highlighted as a company to watch. VA Online gives investors a great opportunity to learn more about how we’re addressing a historically underserved need for cost-effective, high-volume production of composite materials in the automotive and construction markets through our patent-pending advanced manufacturing technology.
About VA Live Online
Venture Atlanta’s mission is to connect companies to capital, resources and talent, enabling attendees to interact with others, watch pitches in real time, stroll the virtual show floor—and more.
During this exciting, two-day event, interested investors can view our virtual booth and request one-on-one meetings with our team. Our virtual booth will remain live for one year after the event, and we will continue to make updates to the page if you’re interested in following our progress.
Register Today
VA Live Online will take place October 21 to 22. To learn more about the event, register or visit our virtual booth, please visit the conference website.