Traditional manufacturing methods for thermoplastic and thermoset composites can produce lightweight, stiff, strong components capable of replacing metals in many applications. But these composites have been:
- Too expensive when scaled to high production volumes
- Overly constrained in their ability to reduce weight while maintaining stiffness
Our patented WEAV3D® process addresses the challenges associated with traditional composite manufacturing methods—including hand layup, resin transfer molding (RTM), automated fiber placement (AFP) and automated tape laying (ATL).
The key to our technology is the use of a customized lattice as the primary reinforcement. We call the lattice structures Rebar For Plastics® and produce them from composite reinforcement tapes on our patented composite weaving machine. The WEAV3D process has two main manufacturing steps—one that takes place on our weaving machine and a second that takes place on standard injection and compression molding presses.
First We Weave
The WEAV3D® process starts with commercially available thermoplastic prepreg tapes. Our standard tape width is 25mm, but we can also customize the tape width depending on the application requirements. The tapes are fed into our composite forming machine, which weaves and consolidates the lattice structure. Automated and continuous, the process reduces waste, cycle time and material handling costs compared to traditional composite reinforcement methods. The machine easily scales to meet automotive part size and production volume requirements.
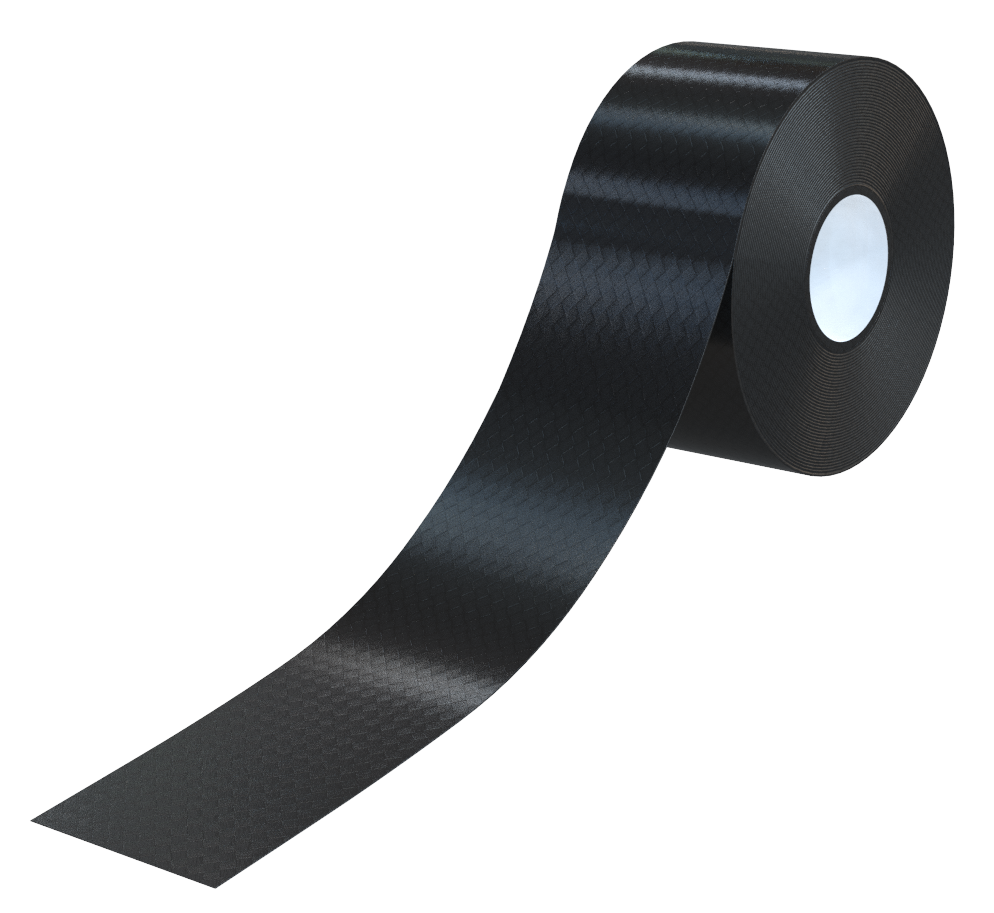
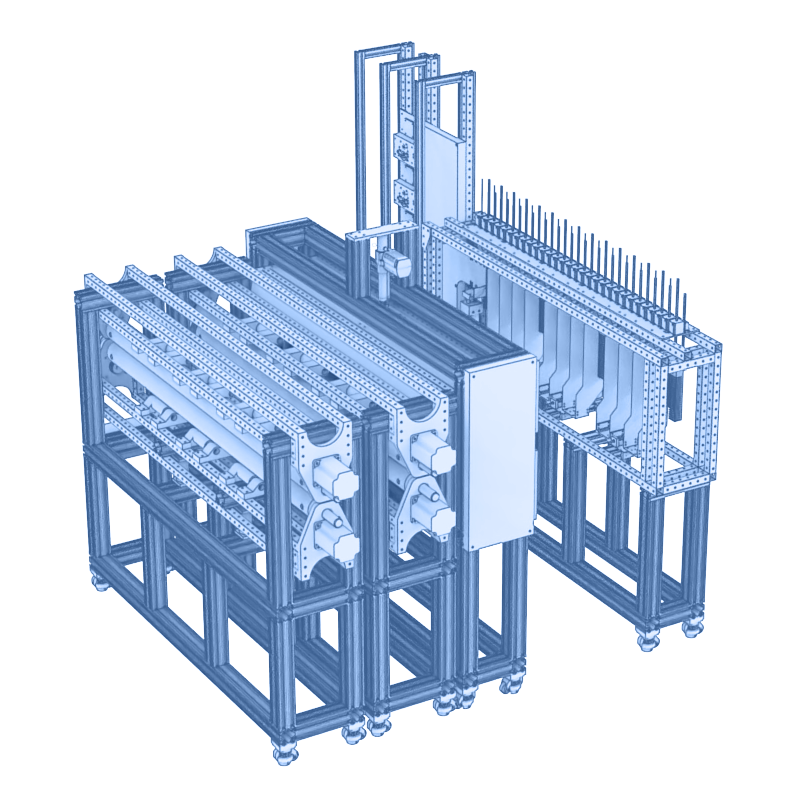
Then We Mold
The WEAV3D® composite forming process scales through integration with existing high-volume composite production methods—including continuous lamination, D-LFT compression molding and injection molding. The composite lattice coming off of the WEAV3D machine can be trimmed and overmolded or insert molded in a continuous production line, enabling cycle times of two to five minutes. Any molder capable of overmolding can quickly adapt to WEAV3D reinforcements with minor process changes and, in some cases, with minimal modifications to existing tooling.
Molders familiar with organosheet composites will find that our process offers a significant potential for reducing trim waste, in part because we can selectively reduce the lattice density in regions of the part with lower strength and stiffness needs.
The Result
Composite parts fabricated using WEAV3D® lattice reinforcement technology can reduce part cost by 30 to 50% compared to high-volume organosheet or tape-laid laminates. The cost saving can climb to as much as 75% when compared to traditional composite processes such as RTM—and even more when compared to hand layup. The process offers design engineers an unprecedented ability to balance the cost, weight and mechanical performance of plastic composites. And the process supports a wide variety of thermoset and thermoplastic materials systems, though the lattices are exclusively thermoplastic.
Composite Forming Steps



