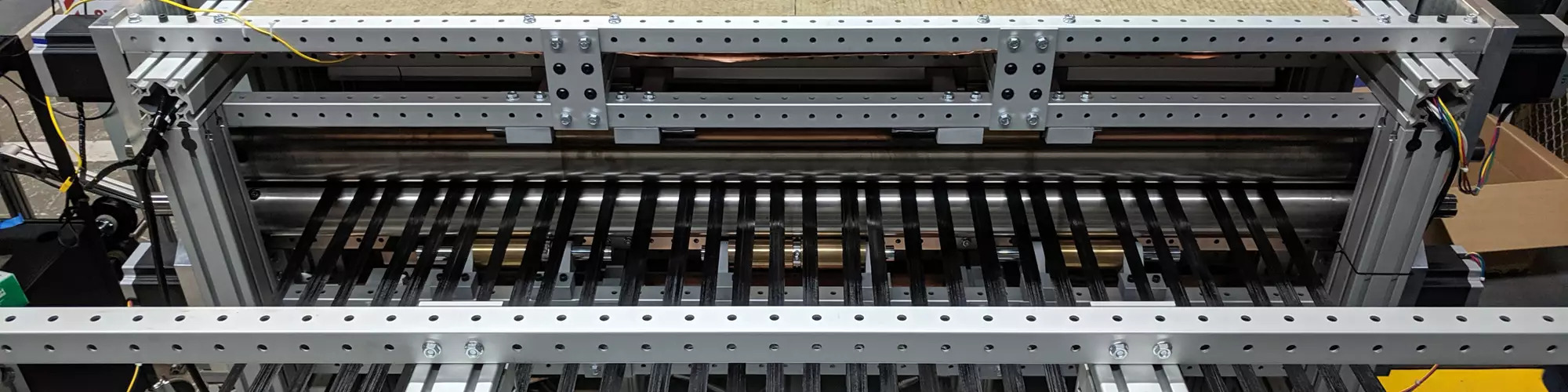
We’re excited to announce we were recently featured in CompositesWorld, a leading source of news and information about fiber-reinforced composites manufacturing. The article takes a deep dive into our locally tunable composite technology—from concept to commercialization.
The article interviews our founder and CEO, Christopher Oberste, who developed the initial concept for our woven composite lattice reinforcement technology while earning his PhD at the Georgia Institute of Technology. From there, the article follows Oberste’s efforts to commercialize the technology and grow WEAV3D into the company it is today.
While the initial plan was to qualify the materials as reinforcement structures in aerospace components, Oberste and his colleagues shifted focus to the automotive and construction markets once they discovered the need for cost-effective, lightweight parts in these industries. “[Companies in these markets] told us that most of the conventional composite manufacturing processes available weren’t able to provide the volume they needed at the costs they wanted,” Oberste tells CompositesWorld.
From there, the WEAV3D technology evolved to become an enabling solution for producing high-volume composite parts at low cost. The result is our Rebar for Plastics® design concept, which now has the following commercial applications:
- Construction: Our composite lattice enables manufacturers of utility products and construction accessories to produce economical, high-quality polymer concrete products, including trench systems.
- Automotive: Oberste and his team have started discussions with U.S. and European tier 1 automotive suppliers and OEMs about using WEAV3D products to reinforce plastic panels in vehicles.
To read the full CompositesWorld article, which takes a detailed look at our composite technology, weaving process and commercialization journey, click here.