IMPROVING NATURAL-FIBER REINFORCED POLYPROPYLENE
Natural-fiber reinforced thermoplastic composites have recently emerged as a lightweight, sustainable alternative to glass reinforced plastics for automotive interior applications such as package shelves, luggage compartment components, load floor and SUV cargo decks. These materials, however, have traditionally lacked sufficient structural performance on their own to meet load and deflection requirements, necessitating the reinforcement of these materials with metallic or back-injected support structures.
The need for additional support adds a weight and cost burden that can be eliminated using the Rebar for Plastics® design approach developed by WEAV3D®. This approach leverages a patent pending composite forming process to produce tailored, woven composite lattices from commercially available thermoplastic prepreg tapes. These lattices provide versatile reinforcement options for a wide range of injection and compression molded plastic parts, imparting extra stiffness and strength while minimizing weight.
In a recent study, WEAV3D lattices were combined with a natural-fiber reinforced polypropylene panel product that is already widely used in automotive interiors. The results showed that the addition of WEAV3D reinforcements to the natural-fiber reinforced components produces dramatic improvements in strength, stiffness and energy absorption.
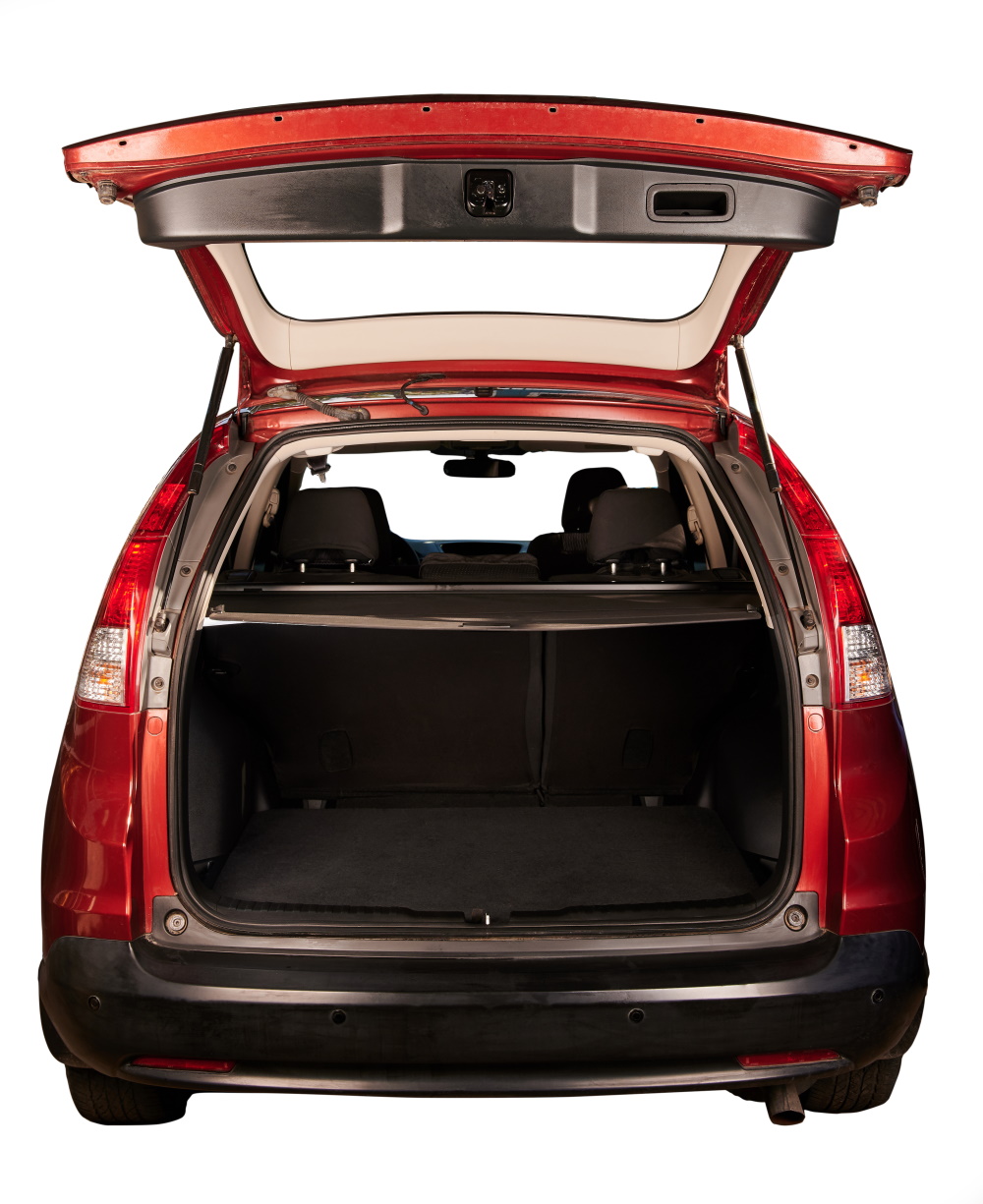
EXPERIMENTAL
The study was conducted on a series of 7-by-7-inch test specimens that differed based on lattice composition and whether the WEAV3D lattice was added to one or two sides of the natural fiber composite. The specimens consisted of:
- Natural-fiber reinforced polypropylene baseline with no lattice reinforcement (NFRP).
- Single-sided WEAV3D lattice composed of glass-fiber polypropylene tape (SSG).
- Single-sided WEAV3D lattice composed of glass-fiber polypropylene tapes and one carbon-fiber tape (SS1C).
- Double-sided WEAV3D lattice composed of glass-fiber polypropylene tapes and one carbon-fiber tape (DS1C).
- Double-sided WEAV3D lattice composed of glass-fiber polypropylene tapes and two carbon-fiber tapes (DS2C).
TEST SPECIMENS
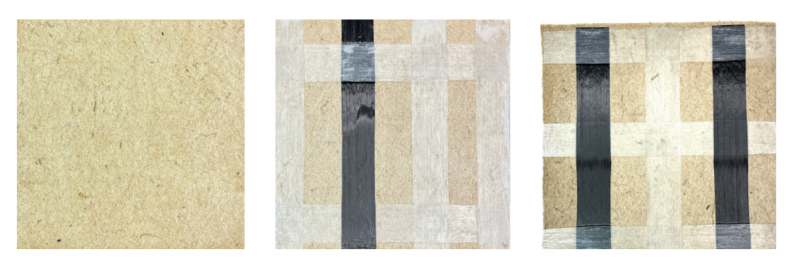
All specimens were prepared by co-forming the natural-fiber composite and the WEAV3D lattice in an oven and then compression molding the resulting hybrid composite, which measured roughly 2-millimeters thick after compression.
Specimens were then subjected to a three-point bending test on an Instron universal testing machine. The tests were independently conducted at Clemson University.
RESULTS
The results of the study show that the addition of WEAV3D lattices improved the flexural strength, stiffness and energy absorption of the natural-fiber reinforced polypropylene panel. Performance increased significantly once a lattice was applied to both sides of the panel, with increasing carbon fiber reinforcement translating to slightly higher stiffness and significantly higher strength.
The gains in mechanical properties from the addition of a lattice enables the elimination of secondary support structures currently required when using natural-fiber reinforced polypropylene in semi-structural applications.
Natural-fiber reinforced polypropylene baseline with no lattice reinforcement (NFRP) |
Single-sided WEAV3D lattice composed of glass-fiber polypropylene tape (SSG) |
Single-sided WEAV3D lattice composed of glass-fiber polypropylene tapes and one carbon-fiber tape (SS1C) |
Double-sided WEAV3D lattice composed of glass-fiber polypropylene tapes and one carbon-fiber tape (DS1C) |
Double-sided WEAV3D lattice composed of glass-fiber polypropylene tapes and two carbon-fiber tapes (DS2C) |